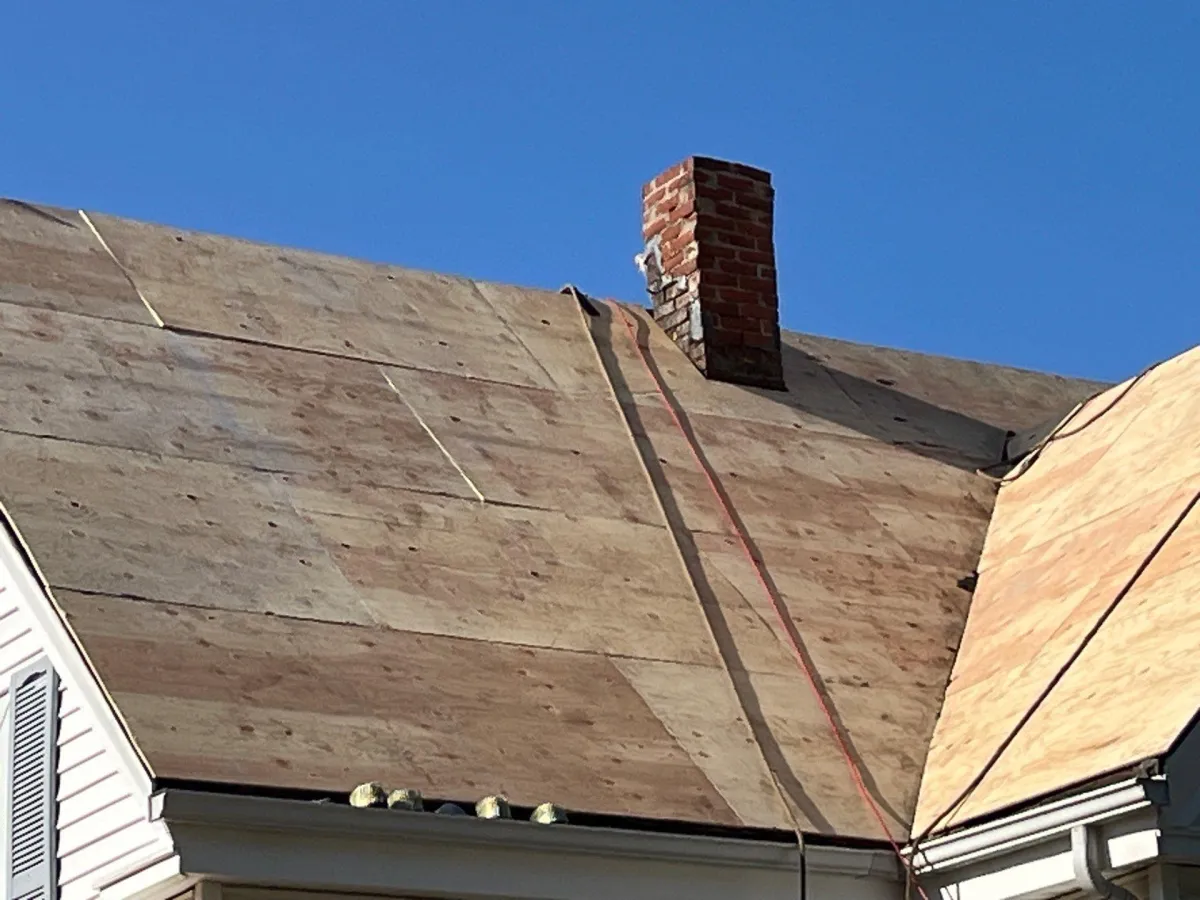
Roofing decking: Sheathing guide & replacement tips
When you think about your roof, shingles or tiles might be the first thing that comes to mind. However, beneath those visible layers lies a critical, often unseen component: the roof decking (also known as sheathing). The decking is the structural foundation that supports the entire roofing system, from the underlayment to the final shingles. Understanding what roof decking is and why it matters is crucial for any homeowner, as its condition directly impacts your roof's longevity, performance, and your home's safety. Masterpiece Roofing breaks down the importance of roof decking.
What is decking/sheathing? Plywood, OSB, or plank boards
Roof decking refers to the flat surface that is fastened to your roof rafters or trusses, providing the structural base onto which all subsequent roofing layers are installed. In residential construction in the United States, the most common types of decking are:
Plywood: A traditional and highly regarded decking material. Plywood is manufactured by gluing together thin layers (plies) of wood veneer in alternating directions. This cross-graining makes plywood very strong and dimensionally stable. It's known for its excellent fastener-holding capabilities, which is crucial for securing shingles against wind uplift. Plywood is typically available in thicknesses from 3/8-inch to 3/4-inch, with 1/2-inch or 5/8-inch being common for roofing.
Oriented Strand Board (OSB): A more modern and widely used decking material due to its cost-effectiveness. OSB is engineered from layers of compressed wood strands, strategically oriented and bonded with waterproof resins. It offers comparable strength to plywood for roofing applications and comes in similar thicknesses. OSB is often identifiable by its distinctive textured, flake-like appearance.
Plank Boards (Solid Sheathing): Common in older homes, plank decking consists of individual solid wood boards (often 1x6s or 1x8s) nailed directly to the rafters, with small gaps between them. While robust, this type of decking presents unique challenges for modern roofing materials designed for solid, continuous surfaces.
The choice of decking material significantly impacts the overall performance and cost of a roofing system.
Differences: Sheet decking vs. Plank decking, Costs & Uses
The type of decking used has implications for installation, cost, and suitability for various roofing materials.
Sheet Decking (Plywood & OSB):
Construction: Comes in large sheets (typically 4x8 feet), allowing for faster installation over large areas.
Cost: OSB is generally more affordable than plywood, making it a popular choice for new construction and budget-conscious roof replacements. Plywood offers superior performance in terms of moisture resistance and fastener retention, often justifying its higher cost for those prioritizing durability.
Uses: Ideal for all modern roofing materials, including asphalt shingles, metal panels, and most tile systems, as it provides a continuous, solid nailing surface.
Plank Decking:
Construction: Individual boards nailed with gaps between them.
Cost: While the existing planks themselves have no direct replacement cost, the labor to install new roofing over them can be higher, and it may require additional steps (like adding new plywood over them) which adds cost.
Uses: Primarily found on older homes built before widespread use of plywood/OSB. While some older roofing materials (like wood shakes) could be installed over spaced planks, modern asphalt shingles and many other contemporary roofing materials require a solid decking surface for proper installation and warranty validation. The gaps can cause shingles to sag, fasteners to miss the decking, and ultimately lead to premature roof failure.
In most modern roof replacements, if plank decking is present, it's often recommended to install new plywood or OSB over it to create a solid, continuous base, or to remove the planks entirely and replace them with sheet decking.
When to replace decking: Signs of rot, gaps >1/8″
The condition of your existing roof decking is a primary factor in determining if it needs replacement. A thorough inspection during a re-roofing project is essential.
Signs of Rot or Water Damage: Any indication of decay, softness, mold, mildew, or visible water stains on the decking (from the attic side or once old shingles are removed) means it needs to be replaced. These areas have compromised structural integrity.
Sponginess or Sagging: If the decking feels soft or spongy when walked on, or if there are visible dips or sagging areas, it's a sign of weakness or water damage and requires replacement.
Cracked or Delaminated Plywood/OSB: Decking that is delaminating (layers separating) or heavily cracked indicates a failure of the material and must be replaced.
Excessive Gaps in Plank Decking: For plank decking, if the gaps between the boards are wider than approximately 1/8-inch, it's usually necessary to install a new layer of solid decking (plywood or OSB) over the planks before installing new shingles. This prevents sagging, ensures proper fastening, and complies with modern shingle warranties.
Insect Infestation: Signs of termite or other wood-boring insect damage necessitate decking replacement in affected areas.
Fire Damage: Even minor charring or smoke damage to the decking should prompt replacement, as its structural integrity may be compromised.
Code requirements: Solid decking for shingle installation
Modern building codes and shingle manufacturer warranties largely dictate the need for solid decking.
Continuous Solid Surface: Most building codes in the United States and virtually all asphalt shingle manufacturers' warranties now require shingles to be installed over a continuous, solid decking surface (like plywood or OSB) for proper installation and long-term performance.
Fastener Holding: A solid deck ensures that roofing nails penetrate and hold securely, which is critical for shingle adhesion and resistance to wind uplift. Nails driven into gaps or weak spots in plank decking will not hold, leading to blow-offs and leaks.
Even Support: Solid decking provides uniform support for the shingles, preventing sagging or "telegraphing" of gaps, which can lead to premature wear patterns and affect the aesthetic of the roof.
Underlayment Performance: Modern underlayments (felt paper, synthetic underlayment, ice & water shield) are designed to be installed on a smooth, solid surface to perform their best as a secondary weather barrier.
If your existing roof has spaced plank decking, a reputable roofing contractor will almost always recommend installing a new layer of plywood or OSB over it to meet current code requirements and manufacturer warranties.
Decking inspection and repair during reroofing
The re-roofing process is the ideal time to thoroughly inspect and address any decking issues, as the old roofing layers have been removed.
Tear-Off Complete: Once all old shingles and underlayment are removed, the bare roof deck is exposed.
Visual and Physical Inspection: A qualified roofing contractor will systematically walk the deck, visually inspecting every section for the signs of damage mentioned above (rot, water stains, sagging, cracks, excessive gaps). They may gently tap or step on areas to detect soft spots.
Moisture Meter Use: For less obvious moisture concerns, a moisture meter can be used to detect elevated moisture content within the decking that might not be visible.
Marking Damaged Areas: Any questionable or damaged areas are typically marked, so they can be easily identified for replacement.
Replacement: Damaged sections of plywood or OSB are cut out and replaced with new material of the same thickness. For plank decking, the decision is made whether to repair individual planks, add an overlay of new decking, or entirely replace the plank system with sheet decking.
Cost Transparency: A professional contractor will discuss any necessary decking repairs or replacements with the homeowner, explaining the reason for the repair and the associated costs before proceeding. This step is often quoted as an "as needed" item in a roofing contract, based on what is found after tear-off.
Decking cost factors & contractor advice
Understanding the cost implications of decking and relying on professional advice is key.
Cost factors for decking replacement:
Material Type: Plywood is generally more expensive than OSB.
Thickness: Thicker decking (e.g., 5/8-inch vs. 1/2-inch) will cost more per sheet.
Extent of Damage: The more square footage of decking that needs replacement, the higher the material and labor costs.
Accessibility: Difficult-to-access roof areas might slightly increase labor costs.
Removal of Old Decking: If existing plank decking needs to be completely removed before new sheet decking is installed, this adds labor and disposal costs.
Contractor advice:
Initial Assessment: A reputable contractor will often provide an estimate for the roof replacement assuming sound decking, but will include a clause for potential decking repairs found during tear-off. They should explain this clearly.
Transparency: They should always inform you immediately if decking replacement is needed, show you the damaged areas, and provide a clear quote before proceeding.
Expertise: Rely on your contractor's expertise to determine the extent of decking damage and the best course of action for replacement or repair, ensuring compliance with local codes and shingle warranties. They understand the nuances of proper fastening and structural integrity.
The roof decking is the unsung hero of your roofing system. Ensuring its soundness and proper installation is fundamental to the overall performance, longevity, and safety of your home.
Is your roof decking ready for its next layer of protection? Masterpiece Roofing provides thorough roof inspections and expert roof replacement services, including meticulous decking inspection and repair. We ensure your roof's foundation is solid, meeting all code requirements and setting the stage for a long-lasting, worry-free roof. Contact us today for a free consultation and let us build you a truly masterful roof from the deck up!